ABSTRACT
Soft robotics is a rapidly emerging area in healthcare and biomedical applications due to recent developments in functional materials and fabrications. This review will focus on the position that soft robotics have in medical application as the result of compliance, adaptability and safe interaction with people in comparison to conventional rigid robots. We also discuss various application areas including surgical instruments, pharmaceuticals, orthopaedic implants and clothing accessories contending that the addition of hydrogels and silicone elastomers makes them more functional and biocompatible. However, several problems remain, some of which are summarized as follows: problems of material endurance, the ability to exert a fine degree of control and the question of the technology’s applicability on a large scale. This review not only presents the solutions to these challenges but also introduces the current trend in the fabrication of sub 1000 μm soft robots and systems with enhanced control. We suggest that by summarizing here some of the most recent advancements and the lines of active research, it is possible to provide the biomedical soft robotics with potential frameworks for new developments. The last section of the article rest on the transformative potential of these technologies for individualized medicine and patient care with a call for interprofessional collaboration to overcome the present obstacles and unlock the full opportunity of soft robotics in biomedical arena.
INTRODUCTION
The use of soft robots in healthcare and biomedical fields is becoming more popular in recent years because of the intrinsic compliant nature of the robots, as well as their adaptability and biocompatibility. These include soft fibrous syringe architects that cannot require electricity or a motor to function, improving health care interaction (Nguyenet al., 2024). This is because the emerging soft magnetic robots offer high safety and fast response with various dexterity that could fit small manipulation in medical applications (Miaoet al., 2024). Moreover, with enhanced scalability in soft robotic technologies there are opportunities for microrobots that work in low Reynolds number to mimic biological microorganisms in motion (Wanget al., 2024).
The latest research work explains how the application of soft robots can revolutionize surgeries involving minimal invasions. For instance, submillimeter-scale soft continuum robots for magnetic control could improve the spatial accuracy during endovascular procedures without causing collateral damage to tissues in the human body (Huet al., 2018). Additionally, self-developed hydrogel skins of these robots offer them enhanced mobility which makes them ideal in reaching invasive lesion (Yuket al., 2016). Another major development includes incorporation of multifunctional sensors into these soft robotic systems. The advancement in flexible skin like sensors has added the capability of continuous monitoring of body information sure to revolutionize treatment methods and diagnosis (Xuet al., 2019).
In this analysis, we will mention several relevant examples to encompass the following evolutionary aspects of the soft bio-microrobots: the design of the base structure, energy systems and biomedical uses (see Figure 1). The first and brief collective reflection will focus on Section 2 on the principles of design. Given that biomimicry serves as the core design approach for these microrobots, they can be categorized into two main groups: biomimetic and bio-cytomeric micro robots. Biologically integrated microrobots are those with jointed structures and flexible segments, showing continuous body like sperms (Figure 1A), whereas biological bots are sperms driven, bacteria powered and algal systems (Figure -B). Subsequently, how each sort is made what materials it uses and the way these sorts are actuated will be discussed. The categories of energy supplied to these soft bio-microrobots include magnetic, acoustic-optical-chemical (as illustrated in the Figures 1C through F) which will be discussed in Section 3. Importantly, catalytic micromotors that operate through chemical reactions for their mobility are excluded from the category of soft and flexible bio-microrobots. Herein, “chemical energy” refers to the energy that is derived from conversion of metabolic processes of the microorganisms or cells as explained hereinabove. Indeed, this energy is ultimately converted into kinetic energy which is required to move the soft bio-microrobots. Such robots can move about using interactions corresponding to flagellar motion or by employing flagellar beating. Depending on the external fields’ treatment, the soft bio-microrobots’ compliant parts can move in a similar manner to flagella to support locomotion. Through physical or chemical methods, microorganisms/cells with flexible flagella and functional materials are merged with these soft bio-microrobots, the motility of which is realized. Oxygen concentration, changes of pressure, chemical concentration gradients, magnetic fields, light and temperature direct the movement of microorganisms or cells to find nutrients avoid dangers and communicate with surrounding milieu. I find that these innate behavioural responses greatly contribute to the directional control of biohybrid microrobots. Section 4 will introduce and synthesize the biomedical applications of soft bio-microrobots across three key areas: targeted drug delivery as depicted in Figure G, biopsy as depicted in Figure H and biofilm eradication as illustrated in Figure I. We will also discuss our outlooks on some issues encountered within the area of soft bio-microrobots at the end of this review.
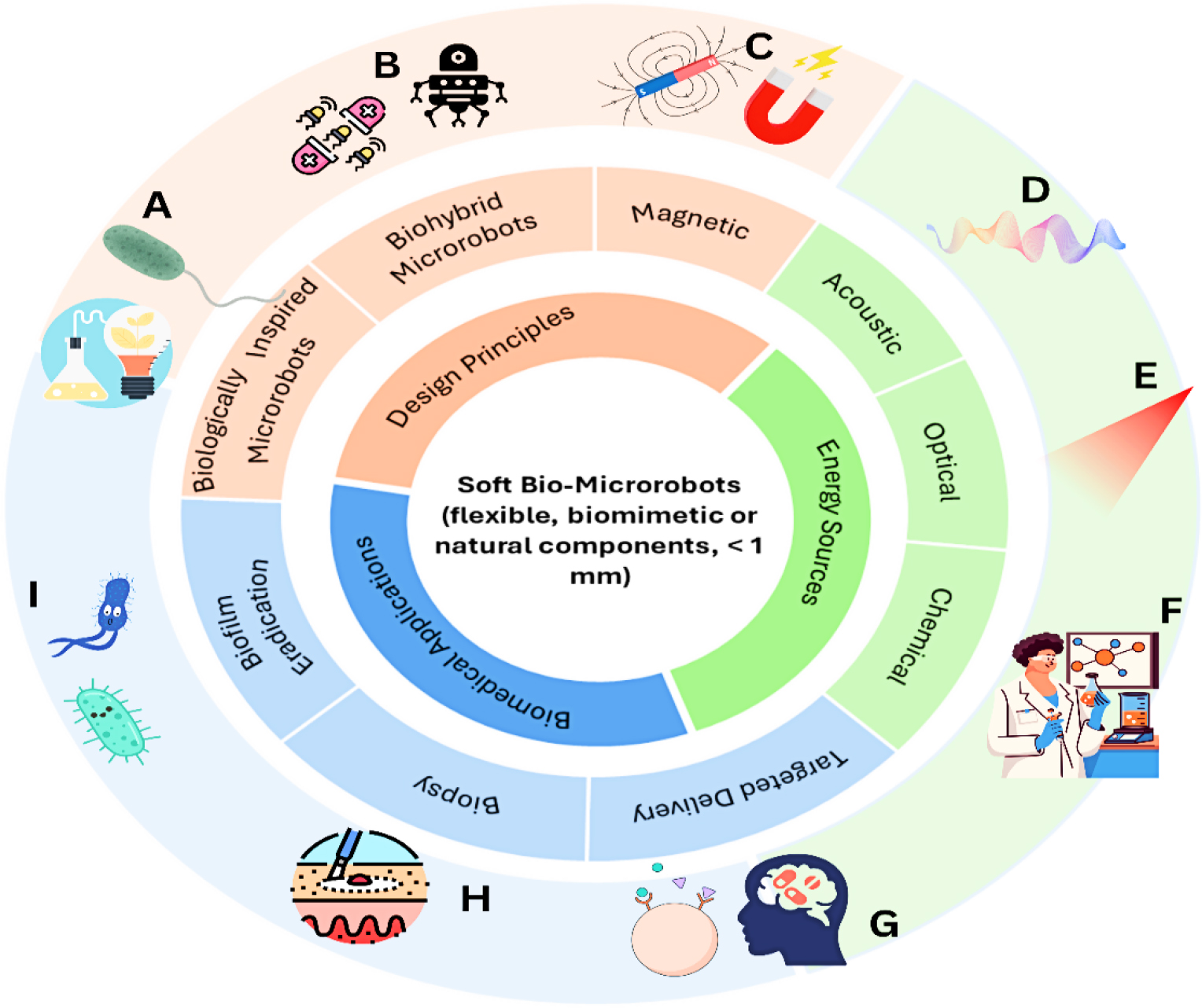
Figure 1:
Schematic illustration of soft bio-microrobots with definition of the design principles, energy sources and biomedical application. Bio-inspired design leads to (A) robotic components with articulated limbs, flexible linkages and unbroken chains. Biohybrid microrobots are developed through (B) sperm-, bacteria-and algae-power. These are the energy sources requisite to activate the soft bio-microrobots are: (C) magnetic, (D) acoustic, (E) optical and (F) chemical power. The biomedical applications include (G) targeted drug delivery, (H)biopsy and (I) destruction of biofilms.
Soft robots are built out of materials that mimic some of the mechanical characteristics of the biological tissue, for example fat, cartilage or skin with modulus ranging between 104 and 109 Pa (Leeet al., 2017; Kimet al., 2022). Some of these materials are gels and functional polymers which in part determine the properties of soft robots (Cianchettiet al., 2018; Sitti, 2018). Interestingly, they enable biologically safe engagements with people while offering multiple DOF for intricate mobilities. This makes soft robots a very applicable area in fields such a biomedical, grasp (Wallinet al., 2018) -and-crawl (Ahnet al., 2019) movements, camouflage and accommodation to soft electronics. It is also able to perform in risky areas, moving through narrow areas and over odd or dangerous ground after catastrophes (El-Atabet al., 2020).
However, there are some problems that need to be solved intact They have made great achievements in biomedical applications, soft grippers and soft electronic devices (Tanget al., 2019). While traditional heavyweight robots may take advantage of a variety of standardized components movable in a standardized matter, soft robots can often have numerous generalized parts (Liet al., 2018). Moreover, soft robots are required to have special structural and motion peculiarities which exert a stress on the role of the actuators in terms of their flexibility, extensibility, contractibility and energy effects. Most current reviews/papers have covered the aspects within the individual categories with detail based on material or actuation type; however, this paper will compare soft robots with a focus on the driving methods, materials used and a few more unexplored applications (Sachyaniet al., 2021).
DESIGN AND MATERIALS FOR SOFT ROBOTS
The field of soft robotics has rapidly evolved, focusing on the integration of innovative designs and materials to create highly functional, adaptable systems. Soft robots, characterized by their compliant structures, have the potential to interact safely with humans and delicate objects, making them ideal for various applications, including medical devices, search and rescue missions and environmental sampling.
Plenty of the motives in soft robotics were triggered by the demand for human collaborative robots which operated in areas of physical human-robot interaction, etc. Usage included robotic forearms within industrial systems and pneumatic powered orthoses for human grasp support. The focus is mostly on motorised or hydraulically actuated robots that are primarily built using stiff material structures for structural integrity and actuation. Such type of robots has the risk of potential harm in workspaces and interaction between human beings and robots has to be supervised. While advancements have been silencing the soft robotics segment, an area of focus is directed in the last years how soft bio-inspired robotics that enable interaction with life span for building new components, apparatuses and systems. However, major obstacles persist in the course of realization of soft bioinspired robots, in terms of creation of new materials and their integration within new still systems. Some of the engineering principles for the development of soft bio-inspired robots are known, but new issues emerge such as the need for more self healing flexible material (Coskuneret al., 2023).
The construction of soft robots involves the use of soft materials such as silicone, hydrogels and polymers. The soft robotics field also encompasses a large number of so-called smart materials capable of self modulations and physical reconstruction while under external stimulation, hence providing information processing resources directly in the body of the robot (often termed as morphological computation). I’m also soft robotics research touches upon structures that include soft and hard parts such as tensegrity structures, foldable robots, origami-based mechanisms and many more. The broadening of the design space here enriches robotics as a whole and makes space available for a range of high novel sensing and actuation systems and thus new applications that were beyond the capability of the traditional robotic systems (Hauser, 2023).
Different mechanical design principles that soft actuators possess allow them to combine passive movements in a non-linear environment and sustained movements in impulsive activation, thus creating a new class of sustainable drive systems. In soft actuators, shape transformation is accomplished by external factors such as heat, light and moisture that activate smart materials including Liquid Crystal Elastomers (LCEs) and hydrogels (Nieet al., 2024).
Design principles
Design principles for soft robots focus on flexibility, adaptability and efficient actuation mechanisms. These principles are essential for enabling soft robots to navigate complex environments and perform tasks that require dexterity.
Material Selection
The soft robots that were developed attempted to break down the big design problem into a number of manageable design problem that are easy to solve or more economical in terms of computational resources. These smaller sub-problems may then be integrated back adjoined into the larger one of design problem case. In this strategy, the designer determines the scope of tasks and computers are employed to solve finer details of the problem (Ligthart and Venter, 2023). Mechanical softness is a common property of most biological tissues. The softness of artificial materials that are intended to mimic these biogenic materials is germane to the emerging field of soft device engineering and, most prominently, for the emerging flexible soft electronics, where lightweight yet mechanically robust electronic devices can be bent, folded, twisted, compressed, stretched, or morphed into arbitrary shapes while their performance remains uncompromised (Yanget al., 2023).
For forward analysis involving significant deformations and material interactions with other materials or barriers, Material Point Methods (MPM) is viable substitutes. MPMs’ hybrid Lagrangian-Eulerian methodology makes it easier for them to manage huge deformations and contacts than FEMs. Topology optimization for elastic materials with significant static deformations has included MPMs. MPMs have been incorporated into topology optimization for soft robot locomotion in more recent research (Satoet al., 2024). The selection of material plays a critical role in the performance of soft robots for a wide range of applications and is fundamental to design and functionality. To respond to the specific needs of soft robotic devices mechanical properties of novel materials that are capable of providing the necessary mechanical properties and allowing complex functionalities are needed. In this literature review (summarise) existing studies on material choice for soft robot materials are presented, with a focus on material science advances and indicating areas of under investigation.
Recent work has highlighted the potential of elastomeric materials in soft robotics with particular significance in the context of pneumatic networks (pneu-nets), which are known to be very reliable and capable of rapid actuation. The work points to the inherent efficiency and speed of elastomers with regard to actuation by demonstrating that they can be used to produce large motion with minimal gas inflation. The life span of soft robots by actuators is enhanced due to the small strain values required at the maximum deformation amplitude, which shows that elastomers are capable of withstanding high deformation rates with limited structural damage. This highlights the importance of soft robotic systems demanding materials which find the right compromise between robustness and elasticity (Mosadeghet al., 2014).
Additionally, the development of soft robotics and the critical role that soft materials play in enabling special robotic capabilities like morphing and stretching. The creation of sustainable robotic systems that replicate biological processes is especially pertinent to the developments in biodegradable and self-healing materials. Material qualities have a major role in the development of flexible robots, indicating that further study into novel soft materials is necessary to satisfy the growing demands for environmental interaction and robustness (Mantiet al., 2016).
In soft robotics, the creation of MXene hydrogels demonstrates the possibilities of stretchy and self-healing materials. These hydrogels are perfect for sophisticated sensing applications because of their excellent sensitivity and tunability. These developments show how the choice of material can improve the functionality of soft robots, especially in responsive robotics and wearable technology (Markvickaet al., 2018). The engineering of elastomer composites containing liquid metal inclusions to meet the twin requirements of mechanical performance and thermal control in soft robotics. These methods demonstrate how creative material design can overcome conventional constraints, enabling flexible, heat-managing soft robots-a critical feature for numerous applications (Zhanget al., 2018). While significant advancements have been made in material selection for soft robotics, several knowledge gaps remain. For instance, the long-term durability of self-healing materials and their performance under various environmental conditions require further investigation. Additionally, the optimization of multifunctional materials that can seamlessly integrate mechanical, electrical and thermal properties in soft robots is an area ripe for exploration. Moreover, exploring the implications of 3D printing technologies in fabricating complex soft structures could enhance the integration of multiple materials, leading to innovative solutions for real-world challenges.
Device Architecture
A few of the early studies focused on the construction and functionality of pneumatic networks, or “pneu-nets,” in soft robotics. By lowering the gas volume required for inflation, they showed how refining the architecture of these networks can improve actuation speed and reliability and produce quick bending motions (from linear to quasi-circular in just 50 ms). These developments are essential for applications that need fast motions, showing how important it is to integrate material qualities with device architecture in order to create soft robots that can function well over long cycles without experiencing performance degradation (Ruset al., 2015).
Methodologies in the field of soft actuators focused on integrating sensing and actuation inside the robot’s body. For small designs that can function well in limited spaces, this integration is essential. They noted the challenge posed by miniaturization and the frequent tendency to design device architecture with a view to achieving an optimum performance. The study of new materials and composites also suggests that the evolution of device architectures is intricately linked to the evolution of soft robotics (Hineset al., 2017).
The concept of combustion-based, functionally graded soft robots, that show how the elastic moduli of various organic elastomers, may lead to naturally compliant robots. In this architectural approach, the focus is on the role of material decisions in device design, to simplify control apparatuses and reduce manufacturing costs. Work, focused on fluidic actuation, demonstrated the way unique properties of soft materials can be taken advantage of in order to perform complex tasks required for sensitive work activities (Bartlettet al., 2015).
Control strategies in active lower extremity prosthesis, with a focus on the challenges of soft robots design and control. The lack of a shared base on which these systems are built means that bespoke control programmes, which incorporate the unique properties of soft robots, will be needed. This shows the inseparability of control and device architecture to the performance of soft robotic systems across various applications (Tuckeret al., 2015).
A novel architectural design to address friction and miniaturization was shown by the development of a submillimeter-scale magnetically actuated soft continuum robot. The robot’s maneuverability is enhanced by the self-lubricating hydrogel skin, which reduces friction and emphasizes the importance of high-performance materials and actuation devices. Research that can provide accurate control of systems in confined environments, particularly in the health sector, is made possible by this work (Kimet al., 2019). In addition, since dielectric elastomer actuators can mimic the properties of organic muscles, they are contrasted with artificial muscles. Since it analyzes complex motions and device architectures that can be adapted based on the needs of the operation, the work is of interest. The power generating ability of these actuators allows a new paradigm for energy harvesting which may enhance soft robotic performance (Baueret al., 2014). Optimization of device architecture is needed to enhance soft robotics performance, flexibility and versatility. Future generation of soft robotic systems that can address challenging problems in many fields will be realized through continuous multidisciplinary research combining material science, engineering and robotics.
Adaptability and Biological Inspiration
The deformability of soft robots is one of the main characteristics that differentiates them from conventional rigid robots, allowing them to deform, compress, climb and deform-mimicking functions exhibited by many biological entities. Soft robotics technology enables morphological adaptation to perform tasks that rigid counterparts are incapable to do. The ability to self-repair and biodegrade enhances performance under conditions of uncertainty and this ability of adaptability to uncertain situations is even more crucial (Trubyet al., 2016). Idealistic properties of soft robotics that can autonomously morph their form and function in response to surrounding environments are reflected by the principles of origami and metamaterials. The self-assembly and tunable capability of soft robots, which enhances their operability, play a significant role in the self-assembly and tunable nature of natural processes (Cianchettiet al., 2018).
Bioinspired electronic skin that enhances tactile sensing of soft robots allowing them to adjust locomotion according to real-time sensing. These advances demonstrate that integration of advanced sensing modalities is essential for developing robots capable of robust, dynamic responses, a feature of biological entities (Boutryet al., 2018). The role of flexibility in robotic surgical systems for MIS and the proposal of standard methods for enhancing surgical performance. Similar to this, a soft exosuit with biological inspiration can improve rehabilitation efforts by simulating human ligaments and providing supportive forces. This is in line with a general trend in soft robotics, in which devices are designed to fit seamlessly into human movement, all by relying on biological principles (Runcimanet al., 2019). Traditionally magnetic soft robotics are studied for their ability to respond to a variety of stimuli. In biomedicine, where robots need to touch live tissues, this is key. Compliant sensing and actuating electronics are further integrated, showing how soft robots may react to changes in their surroundings on their own, increasing their usefulness in practical applications (Kimet al., 2022).
Integration of Actuation
Soft materials like Dielectric Elastomers (DEs), Electroactive Polymers (EAPs), Shape Memory Alloys/Polymers (SMAs/SMPs), electroactive ceramics, Thermoplastic Polyurethane elastomers (TPUs) and hydrogels are used to create soft actuators, which are essential parts of soft robots. Numerous stimuli, such as fluid, thermal, electric, magnetic, light, humidity, chemical, etc., can activate soft actuators. Each actuation technique has unique benefits. For example, fluid actuation has the benefits of low cost, flexibility, simplicity and excellent energy efficiency. Wireless actuation can be accomplished without the use of large pumps and valve control systems thanks to thermal actuation. Significant benefits have been demonstrated by electric actuation in terms of quick reaction, non-loading stimulation and simplicity of integration. Wireless soft actuators can provide distant actuation by magnetic actuation (Tanget al., 2022).
The presented literature provides a critical overview of the soft actuators, including the actuation methods and existing manufacturing types and applications, as shown in Figure 2. This article demonstrates the relations between actuation methods and corresponding motions, which could provide a guideline for actuator design. At the end of this review, the ongoing issues and future ideas of soft actuators are addressed. (Figure ) Describes classifications of soft actuators broadly employed in soft robotics, such as pneumatic actuators, dielectric elastomer actuators, shape-memory materials, hydrogels and other types. Applications in the area of healthcare e.g., wearable assistive devices, artificial muscles) are mentioned.
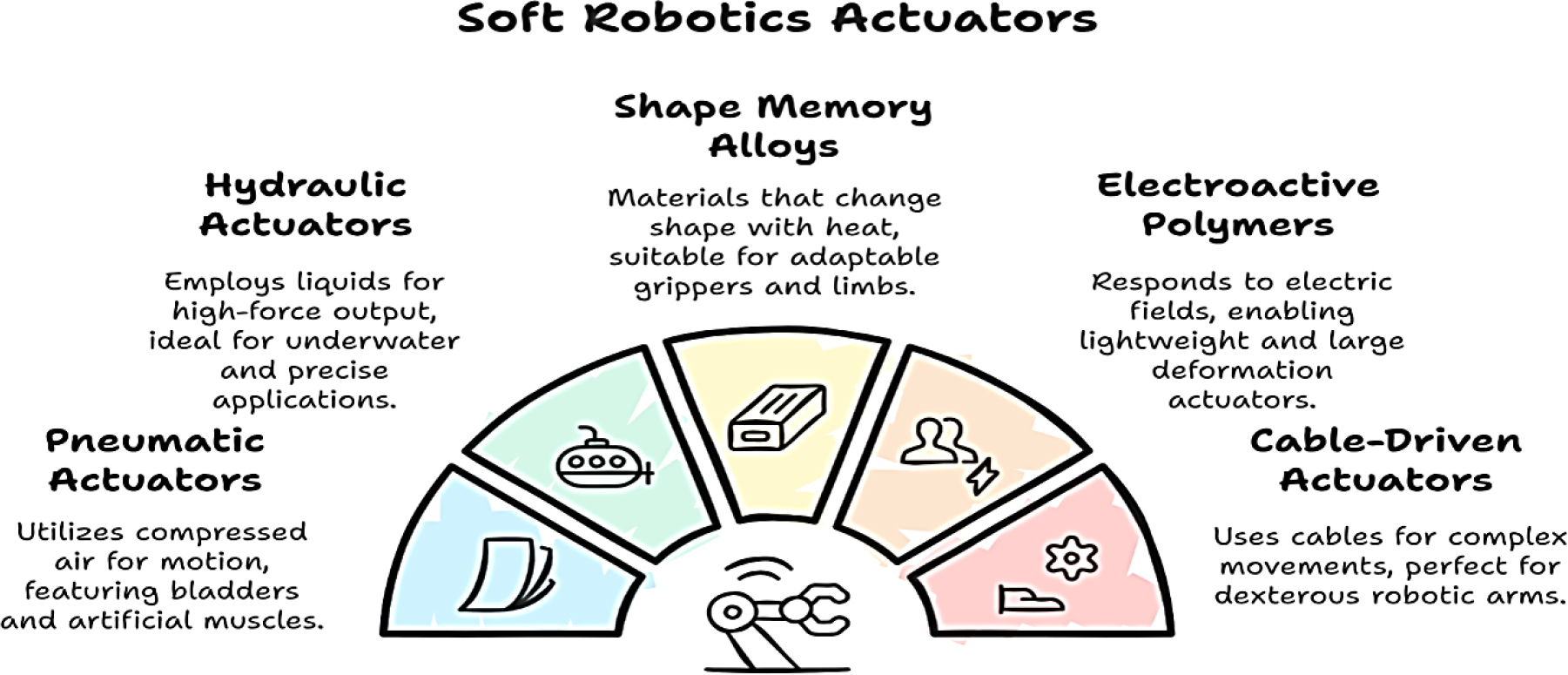
Figure 2:
Overview of Soft Actuators.
METHODS OF ACTUATION
Fluid Actuation
One of the most popular actuation techniques for soft actuators is fluid actuation, which has a low cost, a large output force, a straightforward mechanism and great energy efficiency. Compressible gas and incompressible liquid make up the actuation’s medium, which can be used to alter the pressure inside the sealed area created by flexible inflatable materials (Marcheseet al., 2015).
It is possible to achieve expansion or contraction by altering the volume of the restricted space. Furthermore, as expansion or contraction usually happens first where the stiffness is lowest, the stiffness of flexible materials is the most crucial component for this type of actuation; numerous motions can be accomplished in this manner. However, because it typically requires bulky auxiliary equipment, this actuation technique is rarely employed in wireless actuation (Ilievskiet al., 2011).
Thermal Actuation
Intelligent materials that undergo performance changes when thermal energy is applied are commonly subjected to thermal actuation. These materials can be classified into two categories: those that directly alter the material’s crystal structure in the solid state, like SMAs and those that vary the material’s stiffness, like SMPs. Because of their high recovery stress, SMAs are currently the most commonly used. In particular, the SMA may undergo a modulus change when it transitions from austenite to martensite, which changes shape in response to temperature changes (Kimet al., 2006).
Electric Actuation
Regarding the realization of functions, electric actuation comes in two primary kinds. One is to modify intelligent materials’ stiffness, like Electro-Rheological Fluids (ERF). The alternative is to directly deform intelligent materials like DE, EAPs and Ionic Polymer-Metal Composites (IPMC). When an electric field acts on ERF, its viscosity changes, influencing its stiffness. Dielectric particles and an insulating liquid, like a Newtonian fluid, make up ERF. Along the electric field’s direction, the dispersed dielectric particles are grouped in chains. With a change in stiffness, ERF transitions from a high-viscosity gel state to a low-viscosity liquid state during this process (Mäkelä, 1999).
Magnetic Actuation
By altering the magnetic field, magnetic actuation helps to modify the stiffness of magnetically sensitive materials, which can flex when subjected to external forces. A common magnetic-sensitive substance in this actuation is Magneto-Rheological Fluid (MRF), which is made up of a non-permeable liquid and tiny, soft magnetic particles with high permeability. The viscosity and yield stress of these fluids, which fluctuate in response to variations in the applied magnetic field, are the basis of the MRF stiffness modulation mechanism. Randomly dispersed magnetic particles in the non-permeable liquid create particle chains along the magnetic field’s direction. These chains of particles can produce a significant amount of viscosity and stiffness. Simply substituting elastomers for the liquid medium will get MRF (Wanget al., 2009).
Light Actuation
Light actuation uses an external stimulus to deform the materials via exposure to light. Photothermal and photochemical actuation are the two main types of light actuation and they employ distinct methods. Whereas photosensitive materials are directly activated to realize deformation in the latter, the former is actuated by temperature changes brought on by light. Through the use of photothermal material in the system, photothermal actuation transforms the energy of the absorbed light into heat energy, which causes the polymer material to deform. Photothermal components are added to the polymer matrix to create the photoinduced shape memory polymer material. In essence, this type of material is a form memory substance that is triggered by heat. To create a photoinduced shape memory polymer, the optical fiber is inserted into the polystyrene matrix. Following shaping, a mid-infrared laser is used to irradiate the material (Hirakiet al., 2020).
Humidity Actuation
Humidity actuation is based on the characteristic of moisture-sensitive materials, which can realize internal volume changes by adjusting the environmental humidity gradient to accomplish deformation. Commonly utilized as moisture-sensitive materials, polymer films undergo bending deformation when exposed to water vapor because they absorb and release water, which enables them to react rapidly to changes in ambient humidity. With varying degrees of replacement, cellulose can produce cellulose stearates. Low substitution cellulose stearates exhibit favorable humidity response properties. The cellulose stearate film has the ability to absorb or release water molecules. As a result, the cellulose stearates can bend and fold in a controlled manner. However, a small output force and extremely difficult control are typically associated with humidity actuation. In addition to having trouble carrying out specific tasks, including weight bearing, it cannot provide steady actuation performance over an extended period of time (Zhanget al., 2015).
Chemical Actuation
Other actuations that are triggered by outside stimuli are not the same as chemical actuation. In order to create motion, actuation power is derived from the energy produced by combustion or chemical reactions. A significant amount of gas and heat energy is rapidly produced by combustion reactions, which show dramatic fluctuations and can be instantly transformed into mechanical energy for actuation. However, because of the various elements involved in combustion, it is challenging to precisely control the motions that result and enhance robustness. Additionally, gas may be produced gradually by chemical reactions and can build as a supply of gas to transmit motions. For example, a lot of gas can be produced when liquid solvents are catalyzed. Oxygen is produced via the chemical reaction of hydrogen peroxide that is catalyzed by silver (Bartlettet al., 2015).
Chemical actuation is an internal actuation method that can achieve wireless actuation. However, it cannot be active for very long without external energy input and it is difficult to control the actuation energy.
Acoustic Actuation
Wireless actuation has a new opportunity thanks to acoustic actuation. Acoustic energy has the potential to alter or hang objects in the air. It is hoped that this possible approach will increase the selection of actuation techniques. The idea behind manipulation is to create sound traps with standing waves, which in turn generate suspension forces that keep objects hanging and defy gravity. Additionally, by using ultrasonics to actuate specific liquids, like non-Newtonian liquids, acoustic actuation may develop into a novel actuation technique. A non-Newtonian liquid is forced upward and undergoes deformation when ultrasonic pulses are applied. The actuation concept might be utilized to operate a soft actuator similarly to fluid if elasticity or film could be used to limit the deformation of non-Newtonian liquid (Yanget al., 2018).
Sensing Mechanisms
To transform the input data from the surroundings in which the soft robots are controlled into an output signal that can be recoded, a variety of sensors are produced. The input signals comprise a variety of information that reflects their workplace, such as tactile data, visual patterns and olfactory cues, among others. It is anticipated that the sensors will be sufficiently sensitive to fully transmit the information required for the soft robotics to function autonomously or for people to be more aware of the operated states of the soft robotic systems (Caoet al., 2024).
The development of environmental awareness depends on the tactile sense. When things are touched, mechanical impulses can primarily be transformed into electrical signals. The mechanism allows for the primary classification of tactile sensors into triboelectric, piezoresistive, capacitive and piezoelectric categories. Regarding piezoresistive sensors, the piezoresistive effect modifies the electrical resistance. Variations in capacitance occur for a capacitive sensor in order to detect mechanical signals. The produced voltage in piezoelectric and triboelectric mechanical sensors can reflect mechanical stimuli. In particular, strain or pressure applied to piezoelectric materials can provide an electrical signal, whereas contact, separation, or friction between two materials can produce an electric signal for triboelectric mechanical sensors (Kimet al., 2014). In addition to tactile detection, various stimuli are anticipated to be detected by the intelligent robots in order for them to gather data thoroughly and react appropriately. Cameras or optical sensors are always integrated onto the soft robots to give the systems visual capabilities. Some sensors based on ultrasonic transducers are also used in conjunction to cameras or optical sensors since they can both emit and receive reflected ultrasonic waves to determine an object’s position (Shiet al., 2023).
Chemical sensors are capable of detecting toxic compounds and certain technologies, such as negative Differential Pulse Voltage (nDPV), can reflect the reaction between the sensors’ constituent parts and the hazardous chemicals in addition to changes in peak amplitude (Yuet al., 2022).
A variety of sensors is constructed through which the information of the environment in which the soft robots are operated can be transformed to the output signal which can be replayed. Input signals consist of information reflecting their work environment such as, but not limited to, tactile input, visual pattern and olfactory signal (Table 1). The sensors are anticipated to be sufficiently sensitive to transmit, of course, all the information for the possible autonomous action of the soft robotics, or alternatively for the awareness of humans in order to have a better information about the states operated of the soft robotic systems. It is noticeable that multi-functional sensors are also in high demand to provide the complex information in the environment.
Input | Sensor | Output |
---|---|---|
Mechanical Force/Tactile | Piezoresistive sensors Capacitive sensors Piezoelectric sensors Triboelectric sensors | Change in electrical resistance Variation in Capacitance Voltage generated Voltage generated |
Light/Position/ Reflected ultrasonic signals | Optical sensors Ultrasonic transducers | Electrical Signals Electrical Signals |
Chemicals | Physiochemical sensors Multifunctional and multimodal sensors | Changes of reduction peak Amplitude |
APPLICATIONS IN MEDICAL DIAGNOSIS
Soft actuators have emerged as a transformative technology in the field of medical diagnostics, providing innovative solutions that enhance monitoring, treatment and patient care. This literature review synthesizes relevant research findings that highlight the advancements, applications and future directions for soft actuators in medical diagnostics.
With the introduction of new technologies and methods, the field of medical diagnosis has been transformed. Multimodal imaging, especially of PET/CT and PET/MRI systems, is a significant development. In addition to enhancing diagnostic sensitivity and resolution, these imaging techniques provide a comprehensive assessment of biological function, which is essential for accurate diagnosis and therapeutic planning. For example, development of probes that enable high-resolution imaging and reduce radiation exposure is an example of how these technologies complement one another, highlighting their ability to enhance patient care and humanize personalized medicine (Louie, 2010).
With a variety of health monitoring capabilities that can be provided through soft robots augmented with AI, smart health care (Panget al., 2022) can be positively facilitated. Soft miniature robots in particular are promising candidates for biomedical applications, such as disease diagnosis, controlled drug release, minimally invasive medical treatments and so forth, due to their flexibility in size and ability to move in confined spaces (Caiet al., 2023). It is noticeable that the magnetically controlled soft miniature robots are widely applied in the biomedical fields (Namet al., 2017).
The need for the development of intelligent robots to limit the transmission of infectious diseases has been made apparent by the coronavirus pandemic. One of the most important features of teleoperating robots is the possibility of user-robot interaction offered by Human-Machine Interfaces (HMIs) (Liuet al., 2022). The COVID-19 pandemic has prompted an urgent need for innovative diagnostic technologies that can operate efficiently in high-pressure healthcare environments. A significant development in this area has been the integration of soft actuators into various diagnostic tools, which enhances their adaptability and user-friendliness. This literature review synthesizes research findings highlighting the applications of soft actuators in medical diagnostics during the pandemic, while also identifying knowledge gaps and suggesting future research directions. The COVID-19 diagnostics landscape has changed as a result of the incorporation of cutting-edge technology, especially deep learning algorithms. Effective CT image analysis has been shown to distinguish COVID-19 cases from other types of pneumonia using a completely automatic deep learning approach for diagnostic and prognostic analysis. This study highlights the function of soft actuators in imaging technologies, where they can improve the diagnostic equipment’ adaptation and flexibility, enabling less intrusive and more accurate imaging treatments. Soft actuators might ease the burden on medical personnel by automating imaging procedures, enabling prompt and precise patient evaluations-a crucial function in times of pandemic (Wanget al., 2020).
Soft Robots for Imaging
A significant area of development within soft robotics is its integration with imaging technologies, particularly in medical and rehabilitation contexts. This literature review synthesizes recent research findings on soft robots for imaging, highlighting their capabilities, current applications and identifying gaps that warrant further exploration. Special properties of soft robots (e.g., compliance and retry) are highly relevant for imaging tasks. Its ability to make imaging improvements in the dynamic context of biological systems with fluidic pressurization-driven, intrinsically compliant robots. Due to the capability of these robots to conform to the structure of the soft tissue, they are capable of offering critical real-time image feedback and are suitable for minimally invasive medical diagnostic work (Cianchettiet al., 2018).
The role of microRNAs (miRNAs) has emerged as a pivotal research area, beyond imaging modalities. Since miRNAs can regulate gene expression in many diseases, they are represented as biomarkers. They are candidate candidates for clinical use due to their sensitivity and specificity in the development of an Individualised medical approach. Due to their possible role on patient outcome, the use of miRNAs on clinical routine diagnosis could allow better disease detection and tailoring of treatment strategies as they are further developed (Condratet al., 2020).
Three-Dimensional Printing
Often referred to as additive manufacturing, Three-Dimensional (3D) printing is a type of rapid prototyping technique. This method, which works well for printing intricate structures, prints objects layer by layer using adhesive materials and computer model files (Trubyet al., 2018). The impact of different parameters must be taken into account during printing (Gulet al., 2018). Soft materials were not previously available since only thin film components could be created due to the viscosity and fluidity of the materials; early 3D printing technology could only print rigid materials. a significant advancement in the study of totally soft robots, as opposed to semi-soft ones (Wehneret al., 2016). Their multi-material 3D printing method allowed them to create a soft octopus robot that could both swim and crawl.
The advanced mechanical properties of 3D structures are some of the crucial parameters. The tensile tests, compression tests and dynamic mechanical analysis will be conducted respectively in parallel to the usage conditions of the products. Therefore, dog bone specimens are prepared by thinning to a total width of 14 mm over a 9 mm radius with a length of 45.5 mm and a thickness of 2 mm, with a gauge length of 17 mm and a gauge width of 7 mm. Testing is performed on a universal testing system with a 100 N load cell and custom self-tightening grips. Initial sample lengths will be measured as the distance between grips when testing. Stress is calculated as force divided by cross-sectional area. Samples are strained at a rate of 50 mm/min until torn. All samples will be measured five times (Coskuneret al., 2023). The design, functionality and usability of soft robotic systems have significantly advanced as a result of the application of three-Dimensional (3D) printing technology. Given the flexible architectures and environmental adaptability of soft robotics, 3D printing becomes an essential technique for constructing intricate geometries and customizing material qualities to satisfy particular operating needs. This overview of the literature highlights knowledge gaps and proposes future research directions while synthesizing recent results in the field of soft robotics made possible by 3D printing. Using an integrated additive manufacturing platform, hybrid 3D printing is a new technique for creating soft electronics that combines automated pick-and-place of surface mount electrical components with direct ink writing of conductive and dielectric elastomeric materials. This method involves directly printing conductive electrode and insulating matrix inks in particular configurations. The appropriate electronic circuitry is subsequently created by integrating passive and active electrical components. To do this, an empty nozzle is used in vacuum-on mode to pick up individual components, insert them onto the substrate and then deposit them in the desired location using vacuum-off mode. After that, the parts are joined by printed conductive traces to create soft electronic devices that could be used in biomedical devices, soft robotics and wearable electronics (Valentineet al., 2017).
Three-Dimensional (3D) printing techniques based on light and ink enables quick material design and production without the need for costly equipment, dies, or lithographic masks. They have ushered in a period of manufacturing where soft matter with adjustable mechanical, electrical and other functional qualities can be created under computer control. Innovation in a wide range of applications is being fueled by the growing variety of printed materials and the capacity to programmably control their design and composition across different length scales (Trubyet al., 2016).
A new 3D printing method is presented based on the rheology modifier of Carbomer for direct ink writing of various functional hydrogels. Carbomer is shown to be highly efficient in providing ideal rheological behaviors for multifunctional hydrogel inks, including double network hydrogels, magnetic hydrogels, temperature-sensitive hydrogels and biogels, with a low dosage (at least 0.5% w/v) recorded. Besides the excellent printing performance, mechanical behaviors and biocompatibility, the 3D printed multifunctional hydrogels enable various soft devices, including loadable webs, soft robots, 4D printed leaves and hydrogel Petri dishes. Moreover, with its unprecedented capability, the Carbomer-based 3D printing method opens new avenues for bioprinting manufacturing and integrated hydrogel devices (Chenet al., 2019).
Endoscopic Soft Robots
A new branch called “soft robotics,” which draws inspiration from nature, uses flexible and adaptable materials in a variety of robotic devices. For creating novel endoscopes, this new robotics paradigm offers a number of advantageous features. The materials used in biosoft robotics, such as silicon elastomer, are often biocompatible, which means they are safe to use inside the human body. Additionally, the creation of bendable endoscopes is made possible by amorphous or flexible soft materials, which reduce the possibility of harming delicate soft tissues like the colon wall (Gifariet al., 2019). Because fewer incisions mean less patient trauma and recovery time, Minimally Invasive Surgery (MIS) and Natural Orifice Transluminal Endoscopic Surgery (NOTES) are gradually replacing open surgery. Endoscopy is one of the most popular MIS or NOTES procedures. Originally used merely to observe within the patient’s lumen, endoscopes have evolved into tools for surgical intervention, particularly with the growing popularity of MIS and NOTES (Gifariet al., 2019).
An important development in non-invasive diagnostics is the investigation of exosomal biomarkers. Exosomes, which contain a variety of molecular components, have the potential to detect illness conditions and track the effectiveness of treatments, helping to create individualized treatment plans. The importance of the latest diagnostic technologies with regard to the patient is emphasized by this ongoing study (Linet al., 2015).
Integration of biological part into soft robots is a recent advancement in this area. Due to their capability of responding autonomously to exterior stimuli, the cm-scale bio-bots powered by artificial skeletal muscle strips, are used to show the bio-medical capabilities for tissue engineering and drug delivery. Perhaps the most promising future for research lies in the potential of this biohybrid strategy to lead to soft robots that are not only sensitive to the environment but also capable of performing high levels of control “closed-loop” iteratively during endoscopic procedures Our capacity to build machines and systems that can sense and react to a range of complex and dynamic environments with nonlinear behavior may be transformed by cell-based soft robotic systems. Breakthroughs in 3D printing, tissue engineering and biomaterials, as well as the combination of these technologies, to develop a programmable biological machine at the centimeter scale that can move over a fluid surface. These biological machines can be employed for numerous purposes and represent a significant step towards high-level functional control of soft biorobotic systems due to their elastic properties and living components that can be responsive to external (applied) and environmental (ambient) stimuli (Cvetkovicet al., 2014). Due to low cost, noninvasive nature and excellent patient compliance, oral administration to the GI tract has been used in recent decades. The brief propulsion lifespan of the microrobotic-based capsule limits its ability to be delivered orally in the GI tract. With the benefit of quick and sustained swimming performance, natural algae can successfully overcome this restriction (Zhanget al., 2022).
Biopsy
A biopsy is a medical operation in which a little sample of bodily tissue is taken for additional genetic, cytological, or histological analysis. The liver, breast, lung and skin are among the many organs that need biopsies. Because of their grabbing ability, untethered microgrippers can retrieve objects from a great distance. It has been shown that clusters of live fibroblast cells can be captured by the thermochemically activated microgrippers without compromising the vitality of the cells (Leonget al., 2009). The in vitro biopsy has been performed on a tissue sample from a bovine bladder as well. The enzymatically triggered microgrippers can carry the cells without destroying RNA structure (Bassiket al., 2010). The recovered tissue’s high-quality DNA and RNA can be used for diagnostic purposes. Cell analysis, robotics, biosensing and surgery all depend on single-cell manipulation (Jinet al., 2020). Untethered microgrippers are created using a thermally responsive wax layer to actively grasp or remove individual cells in a biocompatible way. Wax exhibits a spectrum of phase transition temperatures that are pertinent to biology and the human body, therefore it is commonly utilized in food products. Wax is also biocompatible and chemically and physiologically inert. As a result, when doing the biopsy, this microgripper causes no harm to the human body (Gultepeet al., 2013).
Wearable Devices
The word “wearable devices” refers to a broad category of items that are worn or linked to people as wearable technology, which is frequently employed in the medical and monitoring industries. When employed as medical assistants, these gadgets must be lightweight, portable, flexible and capable of producing a sizable torque. Soft robots’ high compliance, adaptability and safety in human-machine contact make them ideal for wearable technology (Banerjeeet al., 2024). For example, a fluid-driven exoskeleton is designed to be worn on the limb and help disabled people with rehabilitation training, such as standing up independently (Caldwellet al., 2007). However, this flexible exoskeleton is only appropriate for those with a particular level of walking ability because it is unable to give adequate output force and support. Origami structures have also been used in wearable technology; due to their low weight, actuators created of them can assist those who are unable to grasp objects of a particular size and weight using pneumatic actuation (Liuet al., 2021). The soft neuroprosthetic hand was able to achieve specific tactile feedback in addition to precise mobility. With a weight of just 256 g, the prosthetic hand can provide real-time feedback to amputees.
Deep learning technologies, particularly Convolutional Neural Networks (CNNs), have revolutionized the analysis of medical images, enhancing the efficiency and accuracy of disease detection. This shift towards AI-driven diagnostics highlights the transformative potential of technology in healthcare delivery (Bakatoret al., 2018).
Another example of technological progress in diagnostics is the creation of colloidal scintillators for medical imaging, which improve X-ray imaging stability and image resolution (Zhanget al., 2019). The relevance of nanotechnology in improving medical diagnostics is further demonstrated by the investigation of Gold Nanoparticles (AuNPs) for their special qualities in therapeutic interventions and diagnostics (Huet al., 2020).
Studies on certain biomarkers for diseases like Acute Kidney Injury (AKI) highlight how important biomarkers are for early diagnosis and tracking the course of the illness, which eventually improves patient care (Piñeroet al., 2020).
FUTURE DIRECTIONS AND INNOVATIONS
Overall, a thorough evaluation of current advancements is conducted, including but not limited to ML, soft robotics actuation systems and intelligence solutions for sensing devices. Due to their high degree of safety, reduced power consumption, lower manufacturing costs and other factors, smart soft robots have advanced significantly along with the AI field’s rapid development (Caoet al., 2024). Traditional rigid robots may do automated tasks precisely and effectively, but due of their rigid structures, they have limitations when handling delicate and fragile objects and could endanger human safety. Consequently, due to their excellent shape adaptation and flexibility, soft robots have garnered a lot of interest in the business. Since obtaining accurate models analytically for soft-bodied robots is difficult, machine learning has been investigated as a potential substitute. An outline of the ways in which soft robots have been modeled and controlled thus far using machine learning techniques. This covers reinforcement learning as well as supervised learning frameworks. The dynamic coupling of robot bodies and their environments, the challenges of obtaining empirical metrics for observability and controllability, the limitations of learned controllers’ transferability to real robots and other issues are all discussed in the article along with the opportunities for the control community to participate (Hauser, 2023). The creation of self-healing hydrogels, which can repair themselves after damage, is a key area of innovation in soft robotics. This feature is essential for improving soft robotic systems’ durability and dependability, especially in uncertain circumstances. By incorporating these hydrogels into soft robotic frameworks, it may be possible to create robust robots that, like living things, adapt to their environment. Furthermore, developments in 3D/4D printing methods for these materials have the potential to completely transform design processes by enabling the creation of intricate, multipurpose systems that replicate the motions of the natural world (Tayloret al., 2016).
Another interesting avenue is the development of flexible materials for electronic skin, or “e-skin.” Due to the requirement for wearing tolerance in applications of morphologically complex material interactions (such as for nanoscience experiments), the ability of these materials to withstand wear in addition to their high mechanical strength is of great significance. The self-repairing characteristics of these materials could be enhanced in future research to respond in a dynamic manner to cues in the environment to enable robots to be adaptive in real-time. In order for human-robot interactions to be natural enough, next-generation e-skin devices capable of enhanced sensory and output functions need to be realized. Due to the ability of SMPs to change their morphology according to an external force, SMPs are at the leading edge of soft robotics. Advanced studies of SMPs could lead to more complex, programmable movement robots, enhancing precision and flexibility for a variety of tasks. Mechanical features of SMPs can be enhanced by functional materials incorporated in them, which will give rise to entirely new applications in the fields of flexible electronics and medical devices. The development of SMPs that can change their shape on their own over time may be made easier by 4D printing research, which would advance soft robotic systems even more (Xiaet al., 2021).
Design principles of biomimetic design are discussed with the moving example of the TacTip series of soft optical tactile sensors in the direction of the future of tactile sensing in soft robotics. Soft robots will be capable of performing complex tasks with greater precision since to the advancement of advanced tactile sensors providing superior sensory feedback. Open sourcing of these technologies is likely to spur both collaboration and rapid innovation that are both critical to better the usability of soft robots for the service and healthcare industries) (Kimet al., 2022). Soft robotics has a promising future through flexible neuromorphic circuits mimicking biological neuronal systems. Sophisticated, adaptive behavior may be realised by enhancing the integration of artificial synapses within soft robotic devices. The compelling applications of the multidisciplinary research, which combines materials science, robotics and biology, are discussed in the context of wearables and neuroprosthetics.
Advancements in soft robots with liquid metal composites open up fascinating possibilities for the development of multifunctional robots. These materials can be adapted for specific applications, e.g., bio-inspired robotics, wearable devices. To achieve enhanced performance and flexibility and to develop robots with instantaneous sensitivity to the surrounding stimuli, future studies should refine formulas (Linget al., 2020). Advances in soft robotics incorporating liquid metal composites offer promising potential for the development of multifunctional robots. These materials can be tailored for specific applications including bio-inspired robotics or wearables. To enhance performance and flexibility and to design robots which can rapidly respond to environmental stimuli, future work is needed to refine formulas. Furthermore, the development of extremely soft and lightweight wearable technology is essential for the upcoming wearable technology generation. Innovative materials will help overcome the drawbacks of large sensors, paving the way for the creation of inconspicuous devices that improve user experience. One of the most interesting emerging fields is the development of bioinspired infrared adaptive soft robotics materials. The performance of soft robots may be enhanced by engineering these materials for specific purposes, including thermal management (Yanget al., 2021). Despite this impressive amount of progress, there remain many unresolved questions in soft robotics. Deep insights into the long-term performance and robustness of soft materials are needed, particularly in challenging and dynamic environments. The creation of standardized testing procedures for soft materials should be the top priority of future research in order to assess their performance throughout time. In addition, as this technology matures, research into the ethical implications of soft robotics within human-focused areas of technology will become critical. Soft robotics has an exciting future as a result of the recent development in actuation principles, materials science and sensing. Solutions to resisting immediate challenges and exploiting new possibilities will need sustained multidisciplinary collaboration and investigation of novel materials and technologies. The applications of soft robots in healthcare, rehabilitation and other areas will expand with the proliferation of their ability to imitate biological function and respond to the environment, enhancing human capabilities and improving standards of living.
Finally, the intrinsically compliant, accommodating and biocompatible properties of soft robots have enabled a significant gain in their applications for biomedical and health care purposes in the past few years. It offers very good safety, fast response time and a dexterity spectrum suitable for some degree of small manipulation in medical applications. Soft robotic technologies have allowed to develop mimicking biological microorganisms in motion, i.e., microrobots. These robots will change the game for minimally invasive procedures and improve their spatial resolution for endovascular applications. without endangering human bodily tissues in the process. These soft robotic systems’ integration of multifunctional sensors has made it possible to continuously monitor bodily data, which holds the potential to transform diagnosis and treatment approaches. With a range of energy sources, including magnetic, acoustic-optical-chemical and biomedical applications in targeted medication administration, biopsy and biofilm eradication, soft bio-microrobots are divided into two categories: biomimetic and bio-cytomeric. Notwithstanding their difficulties, soft robots are a fascinating field for study because of their special qualities and possible uses in grasp-and-crawl motions, camouflage and soft electronics adaption. To fully realize the promise of soft robots in the biomedical and healthcare industries, it is imperative to address current issues and investigate new applications as the area develops.
Soft robotics’ quick progress has created innovative opportunities for the future. Advanced applications in a variety of disciplines have been made possible by the integration of machine learning, soft robotics actuation systems and intelligence solutions for sensing devices. Opportunities for building durable, adaptable and multifunctional soft robots are presented by the development of self-healing hydrogels, flexible materials for electronic skin, shape memory polymers and liquid metal composites. Soft robots will be able to precisely execute complex tasks thanks to biomimetic design elements like the TacTip line of soft optical tactile sensors. Soft robots will also undergo a revolution thanks to the creation of bio-inspired infrared adaptive materials, flexible neuromorphic circuits and sophisticated wearable technology. Future research should concentrate on formula optimization, developing standardized testing protocols for soft materials and examining the ethical implications of soft robotics in human-centered applications in order to overcome the present obstacles and realize the full potential of soft robotics. To advance this sector, interdisciplinary cooperation and the investigation of novel materials and technologies will be crucial. Soft robots’ uses in healthcare, rehabilitation and other fields will grow as their ability to mimic biological processes and adapt to their surroundings increases, ultimately maximizing human potential and enhancing quality of life.
ABBREVIATIONS
LCEs | Liquid Crystal Elastomers |
---|---|
MPM | Material Point Methods |
DEs | Dielectric Elastomers |
EAPs | Electroactive Polymers |
SMAs/SMPs | Shape Memory Alloys/Polymers |
TPUs | Thermoplastic Polyurethane Elastomers |
ERF | Electro-Rheological Fluids |
IPMC | Ionic Polymer-Metal Composites |
nDPV | Negative Differential Pulse Voltage |
MRF | Magneto-Rheological Fluid |
HMIs | Human-Machine Interfaces |
MIS | Minimally Invasive Surgery |
NOTES | Natural Orifice Transluminal Endoscopic Surgery |
CNNs | Convolutional Neural Networks |
AuNPs | Gold Nanoparticles |
AKI | Acute Kidney Injury. |
References
- Ahn C., Liang X., Cai S.. (2019) Bioinspired design of light-powered crawling, squeezing and jumping untethered soft robot. Advanced Materials Technologies 4: Article 1900185 https://doi.org/10.1002/admt.201900185 | Google Scholar
- Bakator M., Radosav D.. (2018) Deep learning and medical diagnosis: A review of literature. Multimodal Technologies and Interaction 2: 47 https://doi.org/10.3390/mti2030047 | Google Scholar
- Banerjee H., Tse Z. T. H., Ren H.. (2018) Soft robotics with compliance and adaptation for biomedical applications and. International Journal of Robotics and Automation [Internet] 33 https://doi.org/10.2316/Journal.206.2018.1.206-4981 | Google Scholar
- Bartlett N. W., Tolley M. T., Overvelde J. T. B., Weaver J. C., Mosadegh B., Bertoldi K., Whitesides G. M., Wood R. J., et al. (2015) SOFT ROBOTICS. A 3D-printed, functionally graded soft robot powered by combustion. Science 349: 161-165 https://doi.org/10.1126/science.aab0129 | Google Scholar
- Bassik N., Brafman A., Zarafshar A. M., Jamal M., Luvsanjav D., Selaru F. M., Gracias D. H., et al. (2010) Enzymatically triggered actuation of miniaturized tools. Journal of the American Chemical Society 132: 16314-16317 https://doi.org/10.1021/ja106218s | Google Scholar
- Bauer S., Bauer-Gogonea S., Graz I., Kaltenbrunner M., Keplinger C., Schwödiauer R., et al. (2014) 25th Anniversary Article: A Soft Future: From Robots and Sensor Skin to Energy Harvesters. Advanced Materials 26: 149-161 https://doi.org/10.1002/adma.201303349 | Google Scholar
- Boutry C. M., Negre M., Jorda M., Vardoulis O., Chortos A., Khatib O., Bao Z., et al. (2018) A hierarchically patterned, bioinspired e-skin able to detect the direction of applied pressure for robotics. Science Robotics 3: Article eaau6914 https://doi.org/10.1126/scirobotics.aau6914 | Google Scholar
- Cai M., Wang Q., Qi Z., Jin D., Wu X., Xu T., Zhang L., et al. (2023) Deep reinforcement learning framework-based flow rate rejection control of soft magnetic miniature robots. IEEE Transactions on Cybernetics 53: 7699-7711 https://doi.org/10.1109/TCYB.2022.3199213 | Google Scholar
- Caldwell D. G., Tsagarakis N. G., Kousidou S., Costa N., Sarakoglou I.. (2007) ‘Soft’ exoskeletons for upper and lower body rehabilitation- Design, control and testing. International Journal of Humanoid Robotics 4: 549-573 https://doi.org/10.1142/S0219843607001151 | Google Scholar
- Cao Y., Xu B., Li B., Fu H.. (2024) Advanced design of soft robots with artificial intelligence. Nano-Micro Letters 16: 214 https://doi.org/10.1007/s40820-024-01423-3 | Google Scholar
- Chen Z., Zhao D., Liu B., Nian G., Li X., Yin J., Qu S., Yang W., et al. (2019) 3D printing of multifunctional hydrogels. Advanced Functional Materials 29: Article 1900971 https://doi.org/10.1002/adfm.201900971 | Google Scholar
- Cianchetti M., Laschi C., Menciassi A., Dario P.. (2018) Biomedical applications of soft robotics. Nature Reviews Materials 3: 143-153 https://doi.org/10.1038/s41578-018-0022-y | Google Scholar
- Condrat C. E., Thompson D. C., Barbu M. G., Bugnar O. L., Boboc A., Cretoiu D., Suciu N., Cretoiu S. M., Voinea S. C., et al. (2020) miRNAs as biomarkers in disease: Latest findings regarding their role in diagnosis and prognosis. Cells 9: 276 https://doi.org/10.3390/cells9020276 | Google Scholar
- Coskuner-Weber O., Yuce-Erarslan E., Uversky V. N.. (2023) Paving the way for synthetic intrinsically disordered polymers for soft robotics. Polymers 15: 763 https://doi.org/10.3390/polym15030763 | Google Scholar
- Cvetkovic C., Raman R., Chan V., Williams B. J., Tolish M., Bajaj P., Sakar M. S., Asada H. H., Saif M. T. A., Bashir R., et al. (2014) Three-dimensionally printed biological machines powered by skeletal muscle. Proceedings of the National Academy of Sciences of the United States of America 111: 10125-10130 https://doi.org/10.1073/pnas.1401577111 | Google Scholar
- El-Atab N., Mishra R. B., Al-Modaf F., Joharji L., Alsharif A. A., Alamoudi H., Diaz M., Qaiser N., Hussain M. M., et al. (2020) Soft actuators for soft robotic applications: A review. Advanced Intelligent Systems 2: Article 2000128 https://doi.org/10.1002/aisy.202000128 | Google Scholar
- Gifari M. W., Naghibi H., Stramigioli S., Abayazid M.. (2019) A review on recent advances in soft surgical robots for endoscopic applications. The International Journal of Medical Robotics + Computer Assisted Surgery 15: Article e2010 https://doi.org/10.1002/rcs.2010 | Google Scholar
- Gul J. Z., Sajid M., Rehman M. M., Siddiqui G. U., Shah I., Kim K.-H., Lee J.-W., Choi K. H., et al. (2018) 3D printing for soft robotics-a review. Science and Technology of Advanced Materials 19: 243-262 https://doi.org/10.1080/14686996.2018.1431862 | Google Scholar
- Gultepe E., Randhawa J. S., Kadam S., Yamanaka S., Selaru F. M., Shin E. J., Kalloo A. N., Gracias D. H., et al. (2013) Biopsy with thermally responsive untethered microtools. Advanced Materials 25: 514-519 https://doi.org/10.1002/adma.201203348 | Google Scholar
- Hauser H.. (2023) Soft robotics: An introduction to the special issue. IEEE Control Systems 43: 28-29 https://doi.org/10.1109/MCS.2023.3253407 | Google Scholar
- Hines L., Petersen K., Lum G. Z., Sitti M.. (2017) Soft actuators for small-scale robotics. Advanced Materials 29: Article 1603483 https://doi.org/10.1002/adma.201603483 | Google Scholar
- Hiraki T., Nakahara K., Narumi K., Niiyama R., Kida N., Takamura N., Okamoto H., Kawahara Y., et al. (2020) Laser pouch motors: Selective and wireless activation of soft actuators by laser-powered liquid-to-gas phase change. IEEE Robotics and Automation Letters 5: 4180-4187 https://doi.org/10.1109/LRA.2020.2982864 | Google Scholar
- Hu W., Lum G. Z., Mastrangeli M., Sitti M.. (2018) Small-scale soft-bodied robot with multimodal locomotion. Nature 554: 81-85 https://doi.org/10.1038/nature25443 | Google Scholar
- Hu X., Zhang Y., Ding T., Liu J., Zhao H.. (2020) Multifunctional gold nanoparticles: A novel nanomaterial for various medical applications and biological activities. Frontiers in Bioengineering and Biotechnology 8: 990 https://doi.org/10.3389/fbioe.2020.00990 | Google Scholar
- Ilievski F., Mazzeo A. D., Shepherd R. F., Chen X., Whitesides G. M.. (2011) Soft robotics for chemists. Angewandte Chemie 123: 1930-1935 https://doi.org/10.3389/fbioe.2020.00990 | Google Scholar
- Jin Q., Yang Y., Jackson J. A., Yoon C., Gracias D. H.. (2020) Untethered single cell grippers for active biopsy. Nano Letters 20: 5383-5390 https://doi.org/10.1021/acs.nanolett.0c01729 | Google Scholar
- Kim B., Lee M. G., Lee Y. P., Kim Y., Lee G.. (2006) An earthworm-like micro robot using shape memory alloy actuator. Sensors and Actuators A 125: 429-437 https://doi.org/10.1016/j.sna.2005.05.004 | Google Scholar
- Kim J., Lee M., Shim H. J., Ghaffari R., Cho H. R., Son D., Jung Y. H., Soh M., Choi C., Jung S., Chu K., Jeon D., Lee S.-T., Kim J. H., Choi S. H., Hyeon T., Kim D.-H., et al. (2014) Stretchable silicon nanoribbon electronics for skin prosthesis. Nature Communications 5: 5747 https://doi.org/10.1038/ncomms6747 | Google Scholar
- Kim Y., Parada G. A., Liu S., Zhao X.. (2019) Ferromagnetic soft continuum robots. Science Robotics 4: Article eaax7329 https://doi.org/10.1126/scirobotics.aax7329 | Google Scholar
- Kim Y., Zhao X.. (2022) Magnetic soft materials and robots. Chemical Reviews 122: 5317-5364 https://doi.org/10.1021/acs.chemrev.1c00481 | Google Scholar
- Lee C., Kim M., Kim Y. J., Hong N., Ryu S., Kim H. J., Kim S., et al. (2017) Soft robot review. International Journal of Control, Automation and Systems 15: 3-15 https://doi.org/10.1007/s12555-016-0462-3 | Google Scholar
- Leong T. G., Randall C. L., Benson B. R., Bassik N., Stern G. M., Gracias D. H., et al. (2009) Tetherless thermobiochemically actuated microgrippers. Proceedings of the National Academy of Sciences of the United States of America 106: 703-708 https://doi.org/10.1073/pnas.0807698106 | Google Scholar
- Li W.-B., Zhang W.-M., Zou H.-X., Peng Z.-K., Meng G.. (2018) A fast-rolling soft robot driven by dielectric elastomer. IEEE/ASME Transactions on Mechatronics 23: 1630-1640 https://doi.org/10.1109/TMECH.2018.2840688 | Google Scholar
- Ligthart P. F., Venter M. P.. (2023) A hierarchical design framework for the design of soft robots. Mathematical and Computational Applications 28: 47 https://doi.org/10.3390/mca28020047 | Google Scholar
- . (2015) Exosomes: Novel biomarkers for clinical diagnosis. TheScientificWorldJournal 2015: Article 657086 https://doi.org/10.1155/2015/657086 | Google Scholar
- Ling Y., An T., Yap L. W., Zhu B., Gong S., Cheng W., et al. (2020) Disruptive, soft, wearable sensors. Advanced Materials 32: Article e1904664 https://doi.org/10.1002/adma.201904664 | Google Scholar
- Liu S., Zhu Y., Zhang Z., Fang Z., Tan J., Peng J., Song C., Asada H. H., Wang Z., et al. (2021) Otariidae-inspired soft-robotic supernumerary flippers by fabric kirigami and origami. IEEE/ASME Transactions on Mechatronics 26: 2747-2757 https://doi.org/10.1109/TMECH.2020.3045476 | Google Scholar
- Liu Y., Yiu C., Song Z., Huang Y., Yao K., Wong T., Zhou J., Zhao L., Huang X., Nejad S. K., Wu M., Li D., He J., Guo X., Yu J., Feng X., Xie Z., Yu X., et al. (2022) Electronic skin as wireless human–machine interfaces for robotic VR. Science Advances 8: Article eabl6700 https://doi.org/10.1126/sciadv.abl6700 | Google Scholar
- Louie A.. (2010) Multimodality imaging probes: Design and challenges. Chemical Reviews 110: 3146-3195 https://doi.org/10.1021/cr9003538 | Google Scholar
- Mäkelä K. K.. (1999) Characterization and performance of electrorheological fluids based on pine oils. Journal of Intelligent Material Systems and Structures 10: 609-614 https://doi.org/10.1106/VMHJ-P9QA-P78F-NM3T | Google Scholar
- Manti M., Cacucciolo V., Cianchetti M.. (2016) Stiffening in soft robotics: A review of the state of the art. IEEE Robotics and Automation Magazine 23: 93-106 https://doi.org/10.1109/MRA.2016.2582718 | Google Scholar
- Marchese A. D., Katzschmann R. K., Rus D.. (2015) A recipe for soft fluidic elastomer robots. Soft Robotics 2: 7-25 https://doi.org/10.1089/soro.2014.0022 | Google Scholar
- Markvicka E. J., Bartlett M. D., Huang X., Majidi C.. (2018) An autonomously electrically self-healing liquid metal-elastomer composite for robust soft-matter robotics and electronics. Nature Materials 17: 618-624 https://doi.org/10.1038/s41563-018-0084-7 | Google Scholar
- Miao J., Sun S.. (2023) Design, actuation and functionalization of untethered soft magnetic robots with life-like motions: A review [Internet]. arXiv; 2024. Journal of Magnetism and Magnetic Materials 586 https://doi.org/10.1016/j.jmmm.2023.171160 | Google Scholar
- Mosadegh B., Polygerinos P., Keplinger C., Wennstedt S., Shepherd R. F., Gupta U., Shim J., Bertoldi K., Walsh C. J., Whitesides G. M., et al. (2014) Pneumatic networks for soft robotics that actuate rapidly. Advanced Functional Materials 24: 2163-2170 https://doi.org/10.1002/adfm.201303288 | Google Scholar
- Nam J., Lee W., Kim J., Jang G.. (2017) Magnetic helical robot for targeted drug-delivery in tubular environments. IEEE/ASME Transactions on Mechatronics 22: 2461-2468 https://doi.org/10.1109/TMECH.2017.2761786 | Google Scholar
- Nguyen C. C., Hoang T. T., Davies J., Phan P. T., Thai M. T., Nicotra E., Abed A. A., Tran H. A., Truong T. A., Sharma B., Ji A., Zhu K., Wang C. H., Phan H.-P., Lovell N. H., Do T. N., et al. (2024) Soft fibrous syringe architecture for electricity-free and motorless control of flexible robotic systems. Advanced Science 11: Article e2405610 https://doi.org/10.1002/advs.202405610 | Google Scholar
- Nie Z.-Z., Wang M., Yang H.. (2024) Self-sustainable autonomous soft actuators. Communications Chemistry 7: 58 https://doi.org/10.1038/s42004-024-01142-1 | Google Scholar
- Pang Y., Xu X., Chen S., Fang Y., Shi X., Deng Y., Wang Z.-L., Cao C., et al. (2022) Skin-inspired textile-based tactile sensors enable multifunctional sensing of wearables and soft robots. Nano Energy 96: Article 107137 https://doi.org/10.1016/j.nanoen.2022.107137 | Google Scholar
- Piñero F., Dirchwolf M., Pessôa M. G.. (2020) Biomarkers in hepatocellular carcinoma: Diagnosis, prognosis and treatment response assessment. Cells 9: 1370 https://doi.org/10.3390/cells9061370 | Google Scholar
- Runciman M., Darzi A., Mylonas G. P.. (2019) Soft robotics in minimally invasive surgery. Soft Robotics 6: 423-443 https://doi.org/10.1089/soro.2018.0136 | Google Scholar
- Rus D., Tolley M. T.. (2015) Design, fabrication and control of soft robots. Nature 521: 467-475 https://doi.org/10.1038/nature14543 | Google Scholar
- Sachyani Keneth E., Kamyshny A., Totaro M., Beccai L., Magdassi S.. (2021) 3D printing materials for soft robotics. Advanced Materials 33: Article 2003387 https://doi.org/10.1002/adma.202003387 | Google Scholar
- Sato Y., Yuhn C., Kobayashi H., Kawamoto A., Nomura T.. Computational co-design of structure and feedback controller for locomoting soft robots [Internet]. arXiv; 2024. https://doi.org/10.1002/adma.202003387 | Google Scholar
- Shi Q., Sun Z., Le X., Xie J., Lee C.. (2023) Soft robotic perception system with ultrasonic auto-positioning and multimodal sensory intelligence. ACS Nano 17: 4985-4998 https://doi.org/10.1021/acsnano.2c12592 | Google Scholar
- Sitti M.. (2018) Miniature soft robots – Road to the clinic. Nature Reviews Materials 3: 74-75 https://doi.org/10.1038/s41578-018-0001-3 | Google Scholar
- Tang X., Li H., Ma T., Yang Y., Luo J., Wang H., Jiang P., et al. (2022) A review of soft actuator motion: Actuation, design, manufacturing and applications. Actuators 11: 331 https://doi.org/10.3390/act11110331 | Google Scholar
- Tang X., Li K., Liu Y., Zhou D., Zhao J.. (2019) A general soft robot module driven by twisted and coiled actuators. Smart Materials and Structures 28: Article 035019 https://doi.org/10.1088/1361-665X/aaff2f | Google Scholar
- Taylor D. L., In Het Panhuis M.. (2016) Self-healing hydrogels. Advanced Materials 28: 9060-9093 https://doi.org/10.1002/adma.201601613 | Google Scholar
- Truby R. L., Lewis J. A.. (2016) Printing soft matter in three dimensions. Nature 540: 371-378 https://doi.org/10.1038/nature21003 | Google Scholar
- Truby R. L., Wehner M., Grosskopf A. K., Vogt D. M., Uzel S. G. M., Wood R. J., Lewis J. A., et al. (2018) Soft somatosensitive actuators via embedded 3D printing. Advanced Materials 30: Article e1706383 https://doi.org/10.1002/adma.201706383 | Google Scholar
- Tucker M. R., Olivier J., Pagel A., Bleuler H., Bouri M., Lambercy O., Millán Jdel R., Riener R., Vallery H., Gassert R., et al. (2015) Control strategies for active lower extremity prosthetics and orthotics: A review. Journal of NeuroEngineering and Rehabilitation 12: 1 https://doi.org/10.1186/1743-0003-12-1 | Google Scholar
- Valentine A. D., Busbee T. A., Boley J. W., Raney J. R., Chortos A., Kotikian A., Berrigan J. D., Durstock M. F., Lewis J. A., et al. (2017) Hybrid 3D printing of soft electronics. Advanced Materials 29: Article 1703817 https://doi.org/10.1002/adma.201703817 | Google Scholar
- Wallin T. J., Pikul J., Shepherd R. F.. (2018) 3D printing of soft robotic systems. Nature Reviews Materials 3: 84-100 https://doi.org/10.1038/s41578-018-0002-2 | Google Scholar
- Wang S., Zha Y., Li W., Wu Q., Li X., Niu M., Wang M., Qiu X., Li H., Yu H., Gong W., Bai Y., Li L., Zhu Y., Wang L., Tian J., et al. (2020) A fully automatic deep learning system for COVID-19 diagnostic and prognostic analysis [Internet]. The European Respiratory Journal 56: Article 2000775 https://doi.org/10.1183/13993003.00775-2020 | Google Scholar
- Wang X., Gordaninejad F., Calgar M., Liu Y., Sutrisno J., Fuchs A., et al. (2009) Sensing behavior of magnetorheological elastomers. Journal of Mechanical Design 131: Article 091004 https://doi.org/10.1115/1.3160316 | Google Scholar
- Wang Z., Klingner A., Magdanz V., Misra S., Khalil I. S. M.. (2024) Soft bio-microrobots: Toward biomedical applications. Advanced Intelligent Systems 6: Article 2300093 https://doi.org/10.1002/aisy.202300093 | Google Scholar
- Wehner M., Truby R. L., Fitzgerald D. J., Mosadegh B., Whitesides G. M., Lewis J. A., Wood R. J., et al. (2016) An integrated design and fabrication strategy for entirely soft, autonomous robots. Nature 536: 451-455 https://doi.org/10.1038/nature19100 | Google Scholar
- Xia Y., He Y., Zhang F., Liu Y., Leng J.. (2021) A review of shape memory polymers and composites: Mechanisms, materials and applications. Advanced Materials 33: Article 2000713 https://doi.org/10.1002/adma.202000713 | Google Scholar
- Xu K., Lu Y., Takei K.. (2019) Multifunctional skin-inspired flexible sensor systems for wearable electronics. Advanced Materials Technologies 4: Article 1800628 https://doi.org/10.1002/admt.201800628 | Google Scholar
- Yang J., Zhang X., Zhang X., Wang L., Feng W., Li Q., et al. (2021) Beyond the visible: Bioinspired infrared adaptive materials. Advanced Materials 33: Article e2004754 https://doi.org/10.1002/adma.202004754 | Google Scholar
- Yang X., Lan L., Pan X., Di Q., Liu X., Li L., Naumov P., Zhang H., et al. (2023) Bioinspired soft robots based on organic polymer-crystal hybrid materials with response to temperature and humidity. Nature Communications 14: 2287 https://doi.org/10.1038/s41467-023-37964-1 | Google Scholar
- Yang Y., Li Y., Chen Y.. (2018) Principles and methods for stiffness modulation in soft robot design and development. Bio-Design and Manufacturing 1: 14-25 https://doi.org/10.1007/s42242-018-0001-6 | Google Scholar
- Yu Y., Li J., Solomon S. A., Min J., Tu J., Guo W., Xu C., Song Y., Gao W., et al. (2022) All-printed soft human–machine interface for robotic physicochemical sensing. Science Robotics 7: Article eabn0495 https://doi.org/10.1126/scirobotics.abn0495 | Google Scholar
- Yuk H., Zhang T., Parada G. A., Liu X., Zhao X.. (2016) Skin-inspired hydrogel-elastomer hybrids with robust interfaces and functional microstructures. Nature Communications 7: Article 12028 https://doi.org/10.1038/ncomms12028 | Google Scholar
- Zhang F., Li Z., Duan Y., Abbas A., Mundaca-Uribe R., Yin L., Luan H., Gao W., Fang R. H., Zhang L., Wang J., et al. (2022) Gastrointestinal tract drug delivery using algae motors embedded in a degradable capsule. Science Robotics 7: Article eabo4160 https://doi.org/10.1126/scirobotics.abo4160 | Google Scholar
- Zhang K., Geissler A., Standhardt M., Mehlhase S., Gallei M., Chen L., Marie Thiele C., et al. (2015) Moisture-responsive films of cellulose stearoyl esters showing reversible shape transitions. Scientific Reports 5: Article 11011 https://doi.org/10.1038/srep11011 | Google Scholar
- Zhang Y., Sun R., Ou X., Fu K., Chen Q., Ding Y., Xu L.-J., Liu L., Han Y., Malko A. V., Liu X., Yang H., Bakr O. M., Liu H., Mohammed O. F., et al. (2019) Metal halide perovskite nanosheet for X-ray high-resolution scintillation imaging screens. ACS Nano 13: 2520-2525 https://doi.org/10.1021/acsnano.8b09484 | Google Scholar
- Zhang Y.-Z., Lee K. H., Anjum D. H., Sougrat R., Jiang Q., Kim H., Alshareef H. N., et al. (2018) MXenes stretch hydrogel sensor performance to new limits. Science Advances 4: Article eaat0098 https://doi.org/10.1126/sciadv.aat0098 | Google Scholar